Wild Metal cleaning technology impresses across a wide range of applications
Wild Metal GmbH of Ratschings in South Tyrol is an acknowledged hydropower industry specialist for sophisticated hydraulic and mechanical engineering – and not without good reason. The company provides for a wide range of hydro-mechanical application scenarios with a comprehensive solution portfolio. The South Tyrolean industry experts’ success is explained in part by their customised solutions, supreme technical standards and flexibility in project management. Wild Metal‘s hydraulic steel structures now offer practical benefits throughout the Alpine region, and on an international stage. The rake cleaning sector provides a comprehensive overview of the technical expertise provided the South Tyrolean hydraulic steel construction professionals.
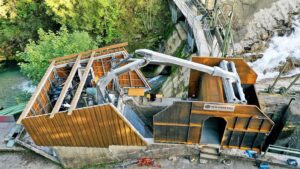
© Wild Metal
As industry specialists in hydraulic steel construction, we understand the individual requirements and challenges facing the sector, offering tailor-made, customer-specific solutions that reflect our flexibility and customer-centricity. The many years of experience and the innovative strength we offer make us the right choice for all hydraulic steel construction requirements – as we make plants more efficient, safer and more sustainable, while meeting the strictest quality standards,” emphasises Wild Metal Managing Director Markus Wild. Furthermore, Wild highlights the central importance of hydro-mechanical engineering at the intake area of a power plant. It’s undoubtedly a good thing if one or two extra percent of turbine and generator output can be achieved via technical optimisation, but if not all of the drive water reaches the machine set due to restrictions at the inlet area, machine efficiency optimisation fails to achieve the desired result.
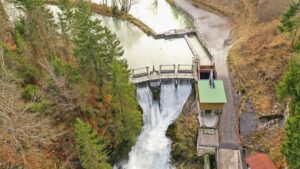
© Wild Metal
Costum-built screen cleaners
Project Manager Daniel Polig points out that Wild Metal trash rack cleaning machinery functions well and is highly reliable, allowing the often extreme demands of alpine hydropower systems to be met: “It’s very important for us to provide robust, low-maintenance, highly-functional infrastructure that also impresses with external aesthetic appeal. Customers can choose from a variety of electro-mechanical and oil-hydraulic solutions. Similarly, environmental compatibility and sustainability play an important role in every project we develop.” Accessibility to spare and wear parts, and to components that require maintenance, is a major priority integrated at the basic design stage. “The robust and stable design of screen cleaning machinery guarantees a long service life, even in situations subject to the most adverse conditions – in turn reducing operating costs and increasing the operational reliability of a system,” Polig explains.
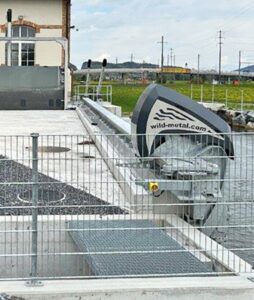
© Wild Metal
Bespoke articulated arm rake cleaner
Last year, Wild Metal realised one of its most recent reference projects in articulated arm screen cleaning technology for the Schattwald power station in the north-eastern part of Tyrol. As part of a large-scale revitalisation project, the old screen-cleaning system at the Vilshofen storage power plant water intake was replaced with a modern articulated-arm screen cleaner using an oil-hydraulic drive. The South Tyroleans equipped the machine with a grab rake, and all the sensors needed for triggering a fully automatic cleaning cycle. “The limited availability of space at the water intake necessitated precise planning and implementation in order to optimise integration of the articulated arm cleaner to work with the rake debris container. The problem was solved with a customised, innovative solution,” says Daniel Polig: “The existing situation had been particularly challenging. It was necessary to dismantle the roof structure of the factory building above the intake screen to make room for the machine‘s articulated arm.” These extreme conditions necessitated a solution tailored to handling floating material removed from the protective screen. Wild Metal designed a special screen debris container with a built-in footbridge protected by a hood structure of Corten steel to meet these requirements. Corten steel is weather-resistant structural steel. Oxidation due to weathering causes a layer of rust to form on the surface. This protects the underlying structure from corrosion damage. After cleaning, the grab rake moves debris into the container positioned behind the protected pedestrian bridge. The machine’s automatic setting offers two operating modes: Normal operation activates a pump unit with an output of 11 kW. In the event of flooding, a second 11-kW-output pump unit is switched on to ensure demand-orientated, flexible and efficient operation. The floodwater set-up allows a full cleaning cycle to be completed in less than 2½ minutes. Special attention was also paid to the energy efficiency of the machine with the installation of a proportional valve hydraulic unit fitted with a variable displacement pump.

© illwerke vkw
Old power plant – new horizontal screen cleaner
Wild Metal supplied an archetypal example of a horizontal screen cleaner in the Swiss canton of St. Gallen for the almost 120-year-old Lienz hydropower plant on the Rheintal inland canal. The project was initiated by plant operator St. Gallisch-Appenzellische Kraftwerke AG (SAK), as the canton required a solution to guarantee a free-flowing continuation of up- and downstream fish migration at the power plant. The project, implemented between October 2021 and November 2022, involved the construction of a technical vertical slot pass fish ladder, and the redesign of the entire intake area. In addition to supplying a trash rack cleaning system, Wild Metal’s scope of delivery encompassed provision of the complete hydraulic steel construction equipment, a weir flap and a special fish ladder. The flap design was reminiscent of a funnel, producing a higher flow velocity towards the end of the funnel, ultimately beneficial for the descent of the fish. SAK project manager Christian Neff describes two significant improvements achieved at the power plant intake on installation of the fish-friendly 18.5 m wide and 1.75 m high horizontal screen, and of the hydraulically operated screen cleaner: “The conversion means the intake area has now been equipped with a horizontal protective screen and associated screen cleaning machine, instead of a coarse screen and a fine screen positioned further downstream. This is an enhancement on an operational level, but also offers benefits for SAK plant operators. Prior to conversion, in the event of blockages the coarse screen had to be laboriously cleaned by hand. Workers had been required to be roped and harnessed for safety reasons. The new screen cleaning system means these efforts are now a thing of the past.”
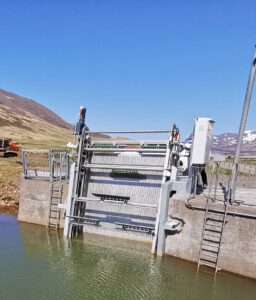
© Wild Metal
Combined Tyrolean weir and Coanda system
Wild Metal again demonstrated its expertise in innovative hydraulic steel construction and trash rack cleaning solutions during the construction of the new small hydropower plant in Dürrenbach, Vorarlberg, which was officially opened in summer 2023. The project, realised by regional energy supplier illwerke vkw, is a classic diversion power plant in which, after being extracted from the watercourse, the headrace water is channelled through a penstock to the 6-nozzle Pelton turbine in the powerhouse. The water intake was fully equipped by Wild Metal, and built at an existing torrent stabilisation stage along the eponymous Dürrenbach. It was not possible to build a desanding basin, usually used for plants of this size, due to the limited space available at the site. Consequently, the South Tyrolean industry professionals were required to provide a special solution. Wild Metal manufactured a Tyrolean weir for the discharge of the headrace water, whose solid protective grid is cleaned by an internally-mounted counter-rake. The fully-automatic screen cleaning system is driven by a total of seven hydraulic cylinders, ensuring reliable weir surface cleaning. The motive water then flows directly to the eight-field ‘Grizzly Power Optimus’ coanda system. Developed and patented by Wild Metal, the system features a largely self-cleaning protective screen for use in the drinking water and hydropower sector. The fine screen has a minimum gap of just 0.6mm and is made of special abrasion-resistant stainless steel. The system is named after, and works according to, the Coanda principle, so debris such as tree needles, moss and fine grains of sand are automatically flushed away from the rake surface by the water flow.
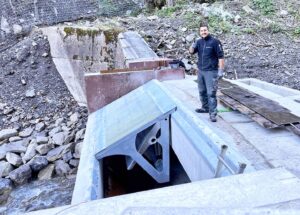
© Wild Metal
An expert partner
In principle, Wild Metal‘s portfolio is as bespoke as the design of every hydropower plant. A more comprehensive list of the South Tyrolean company’s technical solutions currently in operation throughout Europe would far exceed the scope of this article. One thing is certain; hydropower operators seeking industry experts that offer top-quality hydraulic steel construction equipment – and finding Markus Wild and his team – have come to the right place.

© Wild Metal