Austrian industry specialists impress in Vietnam with powerful Francis turbines
The newly-built Dak Di 1 power plant in the Vietnamese province of Quang Nam began generating clean electricity for the first time in November 2022. The Nam Thien Group realised the diversion power plant project to enhance its performance and power generation capacity in the hydropower sector. The operators chose the expertise of the hydropower specialists at GUGLER Water Turbines GmbH to provide the electromechanical equipment. The Austrians supplied two vertical-axis Francis turbines, each designed for a 225.6-m net head and 8.05-m³/s flow rate, and each directly coupled to a synchronous generator. Working at load capacity, each turbine produces over 16.5 MW of bottleneck power. They are the most powerful machines GUGLER has manufactured for Vietnam to-date. The Dak Di 2 power plant is located a few kilometres downstream and was built at the same time as Dak Di 1 and also equipped with GUGLER’s high-efficiency Francis turbines. Together, the two new plants provide bottleneck capacity of more than 48 MW.
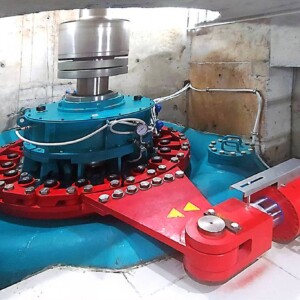
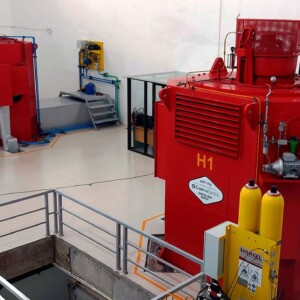
The socialist Republic of Vietnam has a population of around 90 million, and hydropower-generated electricity is one of the central pillars of the country’s electricity supply. More than a third of the electricity generated in the country is produced using water – a renewable resource. Most of the remaining power comes from coal, natural gas and nuclear energy. At present, less than half of the country’s hydropower potential of around 120,000 GWh per year is being exploited, so Vietnam is one of the most promising hydropower markets in the entire south-east Asian region.
TWO NEW HYDROPOWER PLANTS
One of the latest hydropower projects in Vietnam was successfully completed in Quang Nam province, in November 2022. The project was realised by the Nam Thien Group, an enterprise commercially active in the energy, industry, real estate and services sectors. The Nam Thien Group began life in the construction sector, before moving to energy, and now focussing completely on hydropower. Since 2005, the Group has built a whole series of hydropower plants in the Vietnamese province of Lao Cai, and it was involved in the construction of another two hydropower plants in the remote province of Quang Nam, Dak Di 1 and Dak Di 2. Work on these plants, located just a few kilometres apart, started in 2019. They generate electricity by exploiting the hydro-energetic potential of the Thu Bon River.
CHALLENGING CIRCUMSTANCES
GUGLER Water Turbines GmbH is an internationally renowned Austrian hydropower specialist, and provided the electromechanical equipment for both power plants. “The contract for the delivery of four Francis turbines, generators and sub-units was signed in May 2020. Two horizontal-axis machines were delivered for the Dak Di 2 plant, each with a bottleneck capacity of approximately 8.5 MW, each designed for a capacity water flow of 12.75 m³/s and a net head of 98.5 m. The Dak Di 1 power plant was equipped with two vertical-axis turbines, each designed for a bottleneck capacity of 16,527 kW at a net head of 225.6 m, and a maximum water discharge volume of 8.05 m³/s,” says GUGLER’s project manager Thomas Berger. He added that the order for the Dak Di 1 power plant had posed an unusual challenge in terms of design engineering: “A head of more than 220 m and comparatively low flow volume combined to pose a significant challenge in terms of the space required for the vertical-axis machines. Great care was taken when engineering the turbines to ensure that sufficient space was available for future maintenance work.” From an organisational point of view, the restrictions imposed by the Corona pandemic created various hurdles for the project, as Thomas Berger points out: “Around the world, Vietnam was one of the countries with the strictest measures aimed at stopping the spread of the virus. Generally, it was very difficult to obtain an entry permit, and people entering the country had to enter quarantine after arrival.” Weather conditions also posed challenges for the construction company, especially in 2021, when persistent rainfall and subsequent flooding delayed construction progress.
REMOTE SUPERVISION
The turbines were manufactured in Europe and transported to Vietnam by sea. The turbines were delivered in a largely pre-fabricated state to ensure rapid assembly and installation on the construction site. The turbine spirals, the guide vanes and drive trains, impellers included, were pre-assembled at the manufacturing plant. Essentially, due to the vertical-axis design, installation of the machine groups in the powerhouse was carried out in three steps. Initially, the draft tubes were aligned and set in place. Once the concrete had hardened, the turbine spirals were installed on the level above. Subsequently, another level – on which the generators were located – was concreted above it. “In each case, the on-site installation was carried out by local personnel, and monitored by a GUGLER supervisor. It’s worth mentioning that our supervisor was by no means idle during quarantine, being able to observe the most important installation steps and construction site activities via live images. Furthermore, daily logs of the construction site activity were documented on site, and transmitted to the supervisor.”
HIGHLY EFFICIENT TURBINES
The turbine impellers each have a diameter of 920 mm, were milled from forged stainless steel monoblocs and coupled to the generators via separate turbine shafts. “Guaranteeing accessibility to the generator shafts in a vertical set-up means the infrastructure can’t be designed as compactly as with a horizontal machine group. Due to the need for greater distance between generators and turbines, separate turbine bearings were required to ensure vibration-free motion of the turbine runner,” Thomas Berger explains. When manufacturing the turbines, GUGLER relied on proven designs, such as oil-lubricated slide bearings and mechanical seals, to give the operators the greatest possible degree of reliability. Each machine group was equipped with cooling units to ensure an optimal operating temperature for the oil-sump-lubricated bearings. Each of the air-cooled synchronous generators, produced by the Spanish manufacturer Gamesa Electric, weighs over 50 metric tons. According to GUGLER’s project manager, Gamesa has proven itself to be a reliable partner over the past few years. The hot air is passed out along exhaust ducts through the intermediate ceiling in the machine building. The identical machines are also equipped with slide bearings, each being designed for 10.5 kV operating voltage and 17,400 kVA nominal apparent power. GUGLER’s scope of delivery also included the main inlet butterfly valve, and the hydraulic units for the turbine control infrastructure. Electrical and IEC equipment, such as the medium-voltage switchgear, auxiliary power transformers and the diesel-powered emergency generator, were provided by a Vietnamese company. GUGLER specified the machine control logic to guarantee maximum efficiency. The power generated is fed via a newly-laid 110-kV line from the power plant to the mains grid.
VIETNAM REMAINS AN IMPORTANT MARKET
Dry-run plant tests were carried out at Dak Di 1 and Dak Di 2 in the summer of 2022 and, as the penstock still had to be completed, official power plant commissioning took place a few months later, last November. Thomas Berger reported a very positive operating experience registered since completion: “Since commissioning, we’ve only had positive feedback from the operator. There have been no system failures or noteworthy malfunctions so far. Looking back, an interesting project was brought to a successful conclusion – despite the challenging accompanying circumstances, thanks to the good cooperation with the companies and partners on site. At GUGLER we are also pleased to have established our name in Vietnam with higher performance-class machines. Dak Di 1 is the most powerful power plant we have hooked up to the grid in Vietnam to-date.” Project manager Thomas Berger is confident Vietnam will continue to be an important market for GUGLER, as the Austrian industry experts are currently implementing four more projects in the country.