Final commissioning work on Tyrol’s highest new small-scale hydropower plant
This project went right down to the wire! VERBUND’s power plant team only just managed to complete final commissioning work for the new Spiegelwald power plant in mid-November 2023 – before the onset of winter. At around 1,800 metres above sea level in Tyrol’s Zillertal Valley, the power plant utilises water from the upper Zemmbach overflow into the Schlegeis reservoir. It provides an annual yield of around 10.5 GWh of clean electricity using a powerful Francis spiral turbine made by Kochendörfer – the German hydropower specialists. It’s ‘only’ a small hydropower plant in terms of output capacity, but in many respects it bears the hallmarks of larger-scale projects.
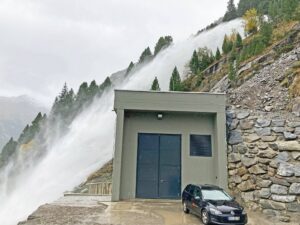
© VERBUND
Schlegeis reservoir in Zillertal Valley in Tyrol is an integral part of the Zemm-Ziller power plant group. The complex of power plants is operated by Verbund Hydro Power GmbH over several stages and reservoirs. It has a capacity of over 1,900 MW, making it one of the most powerful impoundment facility groups in Austria. The Schlegeis reservoir double-curvature arch dam was completed in 1973. Along its curved geometry it’s the longest dam wall of the group at 725 m bank to bank. Water from the Schlegeis reservoir flows via an 8.6 km tunnel to the Roßhag power plant, where four radial pump Francis turbines manage a total output of 230 MW. A sturdily-built toll road with single-lane tunnels, some equipped with traffic lights, leads to the Schlegeis reservoir. At this altitude it’s only open to conventional road traffic from May to the end of October; and at the height of the Schlegeis reservoir every construction project poses key logistical challenges. This was certainly the case at the new Spiegelwald power plant.
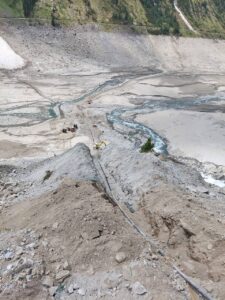
© VERBUND
Stream connection and storage chamber enable power plant realisation
Manfred Kanduth is an engineer, and the overall project manager for the Verbund power plant project. He explains: “In principle, planning for the Spiegelwald power plant was completed ten years ago, but repeated rescheduling delayed construction commencement.” He references accessibility problems in the construction site area, which had required finely-tuned coordination between the individual construction sites; and the extremely short construction season in high alpine terrain. Once planning had been finalised and official approvals granted, initial preparatory work finally began in 2021. The hydraulic source that makes the Spiegelwald power plant possible in the first place is the Zemmbach River. A natural high-altitude alpine watercourse whose water is channelled through the mountain to the Schlegeis reservoir via a tunnel around 6 kilometres long. The water from the Zemmbach River is a key supply source for the Schlegeis reservoir, delivering an average annual water volume of around 60 million cubic metres. Although, hydroelectrically speaking, it had previously been unexploited on its approximately 80 metres descent, everything changed with the new power station. In terms of the power plant project, although essentially the water intake and headrace were already present, it was necessary to install a penstock, a powerhouse, an underwater basin – and a very sophisticated power transmission system. Manfred Kanduth described the difficult conditions: “The Spiegelwald power plant is a small hydropower plant, but the effort and logistical planning involved meant there was little need to fear comparisons with large hydropower projects. In addition to the extensive safety precautions, we regularly faced enormous challenges in terms of weather, access and equipment – and at these heights construction is only possible from June to the end of October.”
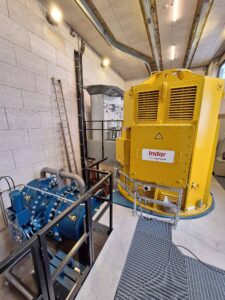
© VERBUND
Gravity tunnel becomes a penstock tunnel
First, to create the penstock, the gravity tunnel was converted into a pressure tunnel. High-pressure GRP DN1400 piping was elevated 65 metres and connected to the tight concrete seal of the pressure tunnel carrying the headrace water to the tunnel exit. A bespoke-manufactured Y-pipe was installed at the tunnel portal to divide the headrace. Depending on regulation and requirements, water can be diverted to an annular piston valve and discharged directly into the Schlegeis reservoir at the level of the tunnel exit. Alternatively, it can be fed into the cast iron underground pipeline to the powerhouse around 40 metres below. There is a transition to an optimised steel inlet pipe at the entrance to the powerhouse, with a DN1200 butterfly valve located in the powerhouse itself, followed by the turbine spiral. Finally, the discharged water reaches the underwater basin via an elbow suction pipe. The first pressure test, held at the beginning of October, was an immediate success, proving that all components of the penstock and tunnel descent corresponded with professional construction standards.
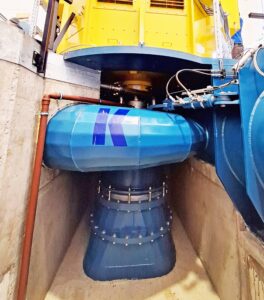
© VERBUND
Energy transmission via submarine cable
Installation of the power transmission infrastructure was a more unusual aspect of the project, as it was only possible to route the power conduit through the Schlegeis reservoir. Consequently, this required the laying of a submarine cable and the correspondingly complicated installation process, as engineer Horst Rass, project manager for electrical and control technology at VERBUND, confirms: “We needed to procure a special steel-armoured cable to ensure it was protected from falling rocks.” The 3.75 km length of submarine cable was installed by excavating a cable trench into the floor of the empty reservoir, laying out the cable on a bed of sand, and sealing the trench. Nevertheless, at the end of August 2023, heavy rainfall undermined the cable bedding and a mudslide ripped the cable in one place. As Horst Rass describes: “Repair procedures were problematic as the affected section of cable was now submerged at around 80 metres below the water surface.” Ultimately, the team’s endeavours were successful. Everyone involved was relieved when the transformer immediately sprang to life during initial commissioning trials.
Cavern acts as a storage facility
Finally, in autumn 2023, cavern tunnel filling commenced, and reaffirmed one of the positive findings of prior geological investigations: More water flows into the tunnel from the mountain than is lost through leaks and fissures. “This is also of relevance since the tunnel has to withstand pressure and fulfil the function of an intermediate storage basin when required. To be more specific, at a length of 6 km it provides around 40,000 m³ of storage volume, allowing it to operate as a small daily reservoir,” explains Verbund’s Dipl.-Ing. Andreas Prackwieser – Project Manager for Mechanical and Hydraulic Steel Engineering. Fellow manager Horst Rass adds: “The system can be stopped and started as needed, especially in winter when there is little water. The tunnel is filled and the full load of water is processed by the turbine in around two hours.” In contrast, when more water is produced than the turbine can accommodate, the annular piston valve is activated, and channels the excess water directly into the Schlegeis reservoir. Andreas Prackwieser points out: “Our top priority was to ensure that water drawn from the Zemmbach River reaches the reservoir. After all, hydroelectric processing takes place via the Roßhag facilities and the main Mayrhofen station along a further descent of 1,000 metres.”
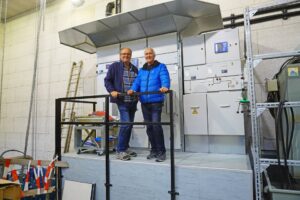
© zek
High-performance turbine
Theoretically, in a year of normal operation, almost 60 hm³ can be channelled to the new Spiegelwald hydropower plant. The turbine, a vertical-axis Francis spiral turbine, was designed by the German hydropower specialists at Kochendörfer to process an expansion water volume of 6 m³/s. A net head of 74 metres generates an output of 4,063 MW. As is standard practice at Kochendörfer, the runner was crafted via CNC milling to guarantee maximum precision, modern hydraulic design aesthetics and supreme performance. In the powerhouse of the Spiegelwald power plant, it drives an air-cooled Indar synchronous generator designed for a rated output of 4.2 MVA. “The generator weighs over 20 (metric) tons, so getting it to the site was accordingly difficult,” Manfred Kanduth recalls.
The machine control technology adapts the inflow at any given moment. “In summer this means that it is controlled via output – as with a target level. In winter, when the water level is low, it can be operated intermittently,” explains Horst Rass. In a regular year, the new machine group is expected to supply around 10.5 GWh of electricity.
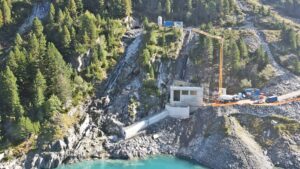
© AFRY
A race against time
However, at the onset of winter last year it wasn’t even a certainty that project completion would be achieved on time. In fact, all three project managers agreed that the final weeks from the beginning of October to mid-November had been a race against time. Up at 1,800 metres above sea level everything stops once the snow comes. Avalanches above the construction sites and the access road make work too hazardous. “In winter, the site can only be reached by helicopter, so it was essential to have completed all electrical and mechanical trials and tests prior to the onset of winter to enable trial operations to be initiated in the spring,” states Manfred Kanduth. Conditions were already wintry when commissioning was carried out in the first week of November. Closing times were set, and this stage was immediately followed by wet commissioning – involving adaptation of the control technology, of protective infrastructure and the synchronising of operations. Although the commissioning phase has not yet been completed, an initial summary offers up positive conclusions: Ultimately, the race against time was won, and all the key objectives were achieved by the responsible parties at VERBUND – and their partners – with a combination of professional coordination, flexibility and team spirit.