No valve is too big for these Austrian industrial and hydropower specialists
Bilfinger Industrial Services GmbH is one of Austria’s largest domestic industrial service providers with headquarters in Linz, and subsidiaries in nine other locations in Austria and neighbouring countries. The company’s portfolio covers the entire value chain – from consultancy, engineering, manufacturing, assembly, maintenance, plant expansions and general overhauls, to environmental technologies and digital applications. Over several decades, Bilfinger has earned itself an excellent reputation as a reliable partner in the hydropower sector, having worked on a great many projects at home and abroad. Recently, the company’s specialists demonstrated their expertise handling large-format closure elements at three large hydropower plants in Switzerland and Austria.
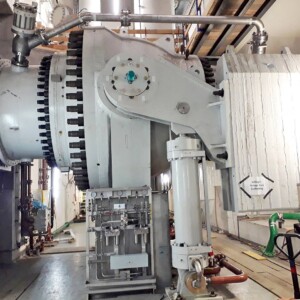
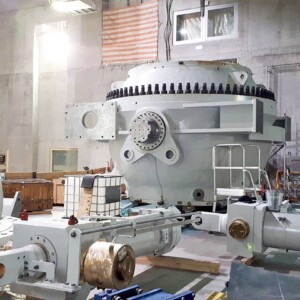
Lago di Vogorno is a reservoir in the Swiss canton of Ticino, serving the Gordola cavern power plant with a total storage capacity of around 105 million cubic metres. The reservoir was formed behind a 220m arch dam, constructed between 1961 and 1965, and is the fourth highest valley dam in Switzerland. Electricity is generated by releasing up to 50m³/s of discharge water from a gross head of 277m into three vertical-axis Francis turbines and one horizontal-axis Pelton turbine, to generate a total power output of just under 110 MW. In a regular year, the Gordola power plant will generate around 230 GWh of green electricity. Last year, 56 years after it was originally completed, the time had finally come to renew the hydraulic steelwork at the base of the reservoir during a planned overhaul. For this purpose, the lake was drained completely for the very first time.
PRECISE TO THE MILLIMETRE
Bilfinger Industrial Services GmbH received an order from Verzasca SA, the power plant operators, to dismantle two butterfly valves housed in a valve chamber. At the same time Bilfinger was commissioned by the manufacturer of the new butterfly valves, Adams Schweiz AG, to carry out the task of installation. Michael Falkner, Bilfinger’s project manager, says the project involved a wide variety of challenges: “To keep power plant down-time as short as possible, detailed planning was required prior to project commencement. One logistical challenge was that the heaviest components had to be transported away – and new ones back again – with a self-driving transporter via the narrow access road from the control centre to the shaft chamber. Inserting and removing components with a crane through a shaft 60m high and with a diameter of 3.6m required precision down to the millimetre. A bespoke fitting ring was installed to compensate axial offset when aligning the new flaps to the existing upstream and downstream connection flanges in the penstock.”
ROTATION REQUIRED
Dismantling and removal of the old components and surrounding technical infrastructure was completed in January last year. The new shut-off devices, including their drive systems, weigh 66 metric tons each, and were installed between mid-March and mid-May. Before the old valves could be removed, a special device had to be installed to enable them to be rotated 60° to be lifted out of the shaft. The new shut-off devices with a nominal diameter of DN2800 were lifted onto new foundation mountings in the chamber. In addition to installation of the new DN2800 butterfly valves, which also had to be rotated by 60° during the lifting procedure, Bilfinger‘s scope of delivery included the installation of an oil-hydraulic control system, and piping for the hydraulic lines. Once installation work had been completed and all seal integrity checks had been made, the operating company refilled Lago di Vogorno, ready for the Gordola power plant to complete the commissioning process.
NEW BALL VALVE FOR A LONG-SERVING POWER PLANT
In 2019, Bilfinger was commissioned by Illwerke vkw, Vorarlberg’s largest energy provider, to install a new ball valve at the Obervermuntwerk I storage power plant, having already provided the armouring of the pressure shaft at the newly-built Obervermuntwerk II pumped storage power plant between 2014 and 2019. Obervermuntwerk I, completed in 1943, has a bottleneck capacity of 30MW and takes advantage of the height difference from Lake Silvretta to Lake Vermunt. At the time of commissioning, the plant‘s two 19-MVA rotary generators were the largest hydropower generators ever manufactured in Austria. Between June and September 2019, Bilfinger provided the replacement DN1500 ball valve required for emergency shutdown, installing it in its location within a valve chamber as the upstream shut-off element for the headrace. On top of assembling components and ancillary systems, order scope also included delivery and installation of the oil and water hydraulic control system.
ORDER COMPLETED IN JUST THREE MONTHS
Bilfinger‘s scope of delivery also encompassed the organisation and execution of all transport logistics and heavy forwarding to the construction site. “This included the ball valve, which – together with the drive – weighs approximately 107 metric tons, as well as the foundation brackets, the hydraulic unit and the pipe components for the ball valve control,“ says Michael Falkner. New foundation mountings had to be installed before the new shut-off valve could be installed. The new ball valve was then lifted in and aligned. A new hydraulic unit and control cabinet also had to be accommodated in the gate valve chamber. Bilfinger manufactured the oil-hydraulic piping, produced the filling and draining lines, and completed the job by pickling the weld seams on the stainless-steel pipelines. In September 2019, after all overhaul measures had been concluded, the long-serving Montafon power plant resumed regular service.
900-MW PUMPED STORAGE POWER PLANT
Step-by-step commissioning commenced at the Swiss Nant de Drance pumped storage power plant in 2021. Since its completion, the plant has been one of the most powerful pumped storage power plants in Europe with a bottleneck capacity of 900MW. An altitude difference of 425m between the Vieux-Emosson reservoir head and that of the lower Emosson reservoir is used to generate electricity. Primarily, the plant was designed to compensate for the fluctuating power output and irregular electricity generation of wind power and photovoltaic plants. The electromechanical equipment is located in an underground cavern. At the heart of the cavern there are six reversible Francis pump turbines. Bilfinger Industrial Services GmbH was contracted by GE Renewable, the manufacturer, to install the each six inlet and outlet ball valves required to shut off the six pump turbines. In a regular year, the new pumped storage power plant is expected to provide about 2.5 TWh of green electricity.
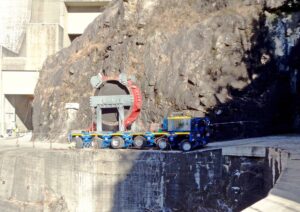
© Falkner Michael
NO ORDER TOO LARGE
Falkner recounted that the project had posed several challenges, especially from a logistical point of view: “Several ball valves had to be installed at the same time. Since the infrastructure was all new, a whole range of suppliers and companies were required to work on the construction site side-by-side. Punctual project completion necessitated precise coordination of the available personnel.” The inlet ball valves each weigh 98 metric tons – even without drives, and were designed with a nominal width of DN2100. Even before the actuators are installed, the outlet ball valves weigh 127 metric tons, and are manufactured with a nominal width of DN2800. The inlet ball valves were designed for a nominal pressure of 65 bar, the outlet ball valves have a pressure rating of 35 bar. As well as installing the large-format shut-off devices, Bilfinger was also responsible for producing the requisite piping for bypasses and drainage lines, and for the installation of the water-hydraulic controls. Work on the order commenced in August 2017, and was completed in September 2019. Bilfinger is justifiably proud that manufacturers and plant operators around the world have relied on the Austrian company’s practical and technical expertise for the implementation of demanding projects for decades. Bundling resources and know-how creates the conditions necessary to provide customers with a complete portfolio of expertise from a single source.