Revitalization – Global Hydro refits old power plants for modern requirements
Around the world today there are thousands of hydropower plants that are outdated or in need of modernisation. The task of transforming old power plants into state-of-the-art operations has created a market worth billions. However, success in this market is only reserved for hydropower companies with an immense wealth of know-how, experience and all the relevant expertise. Global Hydro is an Austrian industry specialist in the provision of flawless turnkey hydropower solutions, and is now in a position to deliver economically-mature technical solutions to guarantee the professional revitalization of every type of hydro- power plant. Under the leadership of Thierry Burckhart, a highly-experienced hydropower professional, Global Hydro’s revitalization department is active on a global scale.
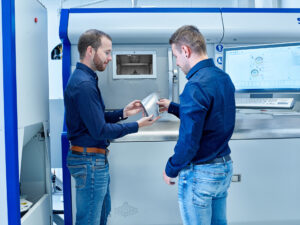
© Global Hydro
There are numerous hydropower plants around the world that have been in operation for 100 years or more, and which fascinate tech enthusiasts to this day. Especially on closer inspection, it’s hard not to admire the engineering achievements of the original hydropower pioneers. Global Hydro is a highly-renowned Upper Austrian hydropower specialist and the company’s Head of Revitalization Thierry Burckhart shares this admiration: “Back then engineers didn’t have computers to assist them; just a pencil, a sheet of paper and engineering expertise; yet they managed to build power plants that operated for decades – and are still in operation. That’s an enormous achievement.” Nevertheless, the experienced hydro industry expert admits even the best maintained plants of the era are now showing their age, and can only meet the complex requirements placed on modern hydropower to a limited extent.
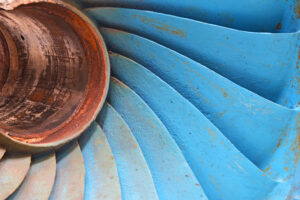
© Global Hydro
A burgeoning revitalization market
Often, as well as suffering the wear damage caused by sustained use down the years, the functionality of old systems is limited by other circumstances, too. Particularly in Central Europe, wherever possible, machine infrastructure was designed to accommodate the passage of the entire volume of a water body. A problem often found with old plants in times of residual water discharge requirements, and dosed volumes for up- and downstream fish passability, is the fact that the old machines are generally too large, so they can no longer guarantee optimum operational efficiency. Another issue is posed at plants built in times of shortage, such as between the two world wars and shortly after the Second World War. During these periods, funding for new, customised and optimised turbines was scarce, so used machines were often reinstalled without further evaluation – operating reasonably well, but never at their best. Subsequently, these circumstances have created a market for infrastructural revitalization in Europe; and an opportunity that companies such as Global Hydro are well-prepared to seize. The all-round hydropower specialists from Upper Austria have identified an opportunity to utilise the expertise they have acquired in this field over decades. Now, consequently, the company’s internal resources and work processes have been adapted and expanded to accommodate this development.
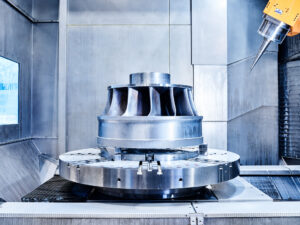
© Global Hydro
Consideration of multiple factors
Old turbines may need to be redesigned, renewed and modernised, blades may have to be replaced and other components repaired. Whatever is required, Global Hydro offers a broad portfolio of services facilitating the provision of an all-round solution package – ranging from the refurbishment of individual parts to the full-scale revitalization of a hydropower plant. Customer benefit is always given the highest priority. Efficiency and performance are not always the only items topping an operator’s list of priorities. As Thierry Burckhart emphasises, several factors play a role in revitalization: “Nowadays, technically speaking anything is possible, but there are two other key factors at the centre of revitalization projects: Firstly, the physical structures at the plant. What do the structure and cubature of the existing infrastructure allow? Are there any restrictions on the remodelling of old listed facilities? This automatically feeds into the second key factor – that of economic viability for the customer. These are precisely the questions we discuss with customers to ensure we develop the right concept for each individual revitalization project.”
Expertise and references required
Thierry Burckhart, the experienced Global Hydro hydropower professional is convinced that today, as well as the technical skills, a great deal of experience is required: “Nothing is possible without many years of expertise, and the references that go with it.” Every ‘greenfield’ project – a new project built from scratch – is less demanding and complex than the revitalization of an existing plant. Both in terms of technical realisation and, ultimately, with regard to areas such as documentation and customer interaction. Furthermore, as Burckhart explains, revitalization projects in particular rely on in-depth hydropower expertise. Solutions are identified with respected fellow specialists who know their plants inside out, and can discuss sophisticated issues eye-to-eye. Global Hydro is ideally equipped in this respect, having an exceptionally efficient design and manufacturing side, and being able to rely on a young, highly-trained team with interdisciplinary capabilities, knowledge of the respective markets and an excellent international contact network.
A single point of contact
In recent years, numerous reference projects have provided impressive proof of what this team is capable. Burckhart recalls a revitalization project just a few years ago, carried out on a turbine built over 100 years ago: “Professional modernisation enabled nominal output to be increased by 36 % and annual production by 23 %.” He also mentions a project in Switzerland that achieved a double-digit percentage output increase by improving runner geometry. “One item in Global Hydro’s favour is our extensive production line, enabling us to manufacture virtually every core component ourselves, beginning with proprietary runner design and certainly not ending with our own butterfly valves. Against this background, we have the best-possible control over an order – from start to finish. Moreover, as a turnkey specialist, we provide solutions without needing to coordinate with external firms. Heinz-Peter Knass, Managing Director of Global Hydro, explains how this allows the customer to manage an entire project through a single contact person.” This is claim that’s true for the D-A-CH region, and the rest of Europe. Over the past few years and decades, Global Hydro has built up an excellent reputation within the industry as an expert provider of turnkey solutions. It’s a reputation upon which the company is able to build in the field of revitalization.
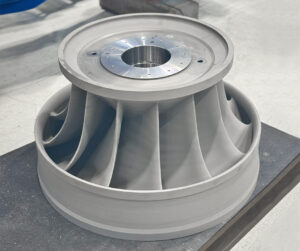
© Global Hydro
Forward-thinking reverse engineering
Global Hydro’s many years of experience have also equipped the company to deal with machines originally built by other manufacturers. The company’s familiarity with all types of turbines, various sub-variants and their components, enables it to restore them to ‘as-good-as-new’ with ultimate professionalism.Sometimes the original plans for old power plants can no longer be located, but as Thierry Burckhart explains, this is not a significant obstacle for Global Hydro professionals: “The tools available to us today enable us to reverse engineer the construction process – and work in reverse gear, so to speak.” This means the machines are dismantled – without documents on the original geometry – and dissembled into their individual parts. Each of the parts is measured is subjected to ultra-precise measurement, and these data are used by engineers to generate new design drawings. In the course of further material testing, the necessity of replacing a component is analysed if hairline cracks or wear are detected. Of course, the Upper Austrian hydropower specialists use only high-performance, state-of-the-art materials. Only the highest quality steels are used to guarantee component longevity. Innovative coatings like HVOF can also be applied if necessitated by drive-water sediments. Strict quality management guarantees Global Hydro’s solutions always meet the highest quality standards.
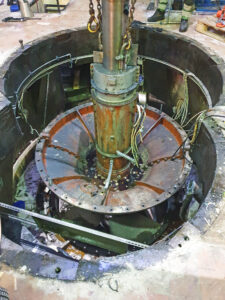
© Global Hydro
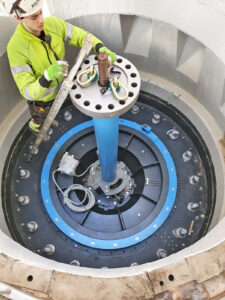
© Global Hydro
XXL runners? No problem!
Global Hydro’s versatility in the revitalization segment is also reflected in the ability to accommodate a comprehensive range of runner dimensions. According to Thierry Burckhart, who has been working successfully in the hydropower sector for 37 years: “In the revitalization sector it’s no problem for us to handle runner sizes from small to large, even up to a capacity of 50 MW. We recently completed a project in Austria that required two 22.5 MW pump turbines, and can refer back to projects in Scandinavia with extremely large output ranges.” Thierry Burckhart continues, pointing out that Global Hydro has been very successful in positioning its new EVO turbine series on the market, especially in Scandinavia, where old propeller turbines are now gradually being replaced. The new Kaplan EVOline turbine is ideal for the purpose, as it minimises the need for conversion work on existing structures – as does the Francis EVOline, too.
Into a new era with HEROS
Turbine control systems also deserve special attention as they bear primary responsibility for ensuring turbines constantly operate at optimum capacities. In this regard, one key consideration is the fact that innovation in control technology and software development is far more rapid than in turbine construction. Resultantly, new technologies are constantly appearing on the market, enabling operators to maximise plant yield and minimise maintenance intervals. Furthermore, the energy market is in a constant state of flux, continuously offering up new opportunities for yield optimisation. There are new opportunities to optimise energy yields, and ultimately a plant’s regular overall output, as well as new demands and requirements, such as new grid codes. There are certainly enough reasons today for hydropower operators to guarantee their control systems are up-to-date. The Global Hydro HEROS power plant management system is a state-of-the-art digital solution for the operational handling of hydropower infrastructure. It controls, monitors and optimises the entirety of plant operations. The latest version of HEROS can be equipped with an IoT (Internet of Things) gateway to transmit the operating data to dedicated cloud infrastructure, from which it is read and used for two purposes: The first is the analysis of data supported by machine learning to maximise production and detect any anomalies at an early stage. Early detection of deviations in readings can reduce maintenance time and repair costs, and lower the risk of failure significantly. The second is the use of data to visualise situations in the IoT SCADA HEROS Connect system. “HEROS Connect allows operators to visualise, analyse and control all systems on a single platform. The software facilitates the utilisation of previously unexploited synergies,” Managing Director Heinz-Peter Knass declares. Another significant benefit offered by the system is that both solutions – machine learning-based data analysis and HEROS Connect – can be used regardless of the control system manufacturer, so it is not necessary to install a HEROS control system. This provides a simple way of modernising outdated, obsolete control systems, particularly in the event of comprehensive revitalization, while keeping the requisite financial investment, construction work and downtimes to an absolute minimum.
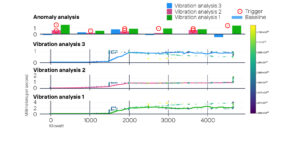
© Global Hydro
Alternative solutions
Global Hydro’s expertise in handling international revitalization projects has also enabled it to play an active role on the American and Canadian markets, where the technical requirements are somewhat different: Especially at the beginning of the 20th century, so-called ‘camelback’ turbines were frequently installed at low-pressure locations on the North American continent. Since the Kaplan turbine had not yet been invented, or become the all-conquering installation on the global market, camelback turbines were the only viable technical solution for locations with high flow rates and low heads. The name ‘camelback’ refers to the fact that several Francis runners are installed on a single shaft, usually two or four, occasionally even more. The name ‘camelback’ turbine refers to the arrangement of the intake manifolds. This specific type of turbine has reached the end of its working life in many parts of North America, and has gained a reputation of being inefficient, prone to faults and malfunctions, and in need of modernisation. Consequently, Global Hydro is keenly aware of the revitalization potential in this segment.
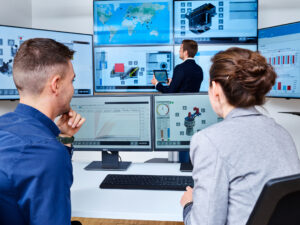
© Global Hydro
Overall economic efficiency
Fundamentally speaking, the vast majority of revitalization projects focus on two premises: increasing efficiency and minimising downtimes. At Global Hydro engineers utilise their entire portfolio of services to this end. Thierry Burckhart summarises: “We consider the overall economics of every project. So alongside all the technical issues, there’s also the question: How much operational downtime will there be during plant conversion? Only when all aspects are taken into account is it possible to compile the perfect revitalization package for a customer.” Similarly, Managing Director Heinz-Peter Knass confirms that in the years ahead emphasis will be placed on revitalization. “Strictly speaking, we have been providing revitalization services for decades, but for a long time there was no separate department and no specialised staff exclusively dedicated to this important area. This has changed with the establishment of the revitalization department at Global Hydro due to the sharp increase in demand. Customers can rely on the quality and services we guarantee for green field and revitalization projects.” For more information, please contact our experts: revitalization@global-hydro.eu