German screen cleaning technology proves its worth in Papua New Guinea mine hydropower plant
Since late summer 2023, technology “made in Germany” has been removing floating debris from the intake area of a small hydropower plant in Papua New Guinea that provides energy for the local Ok Tedi gold and silver mine. The new screen cleaning system was supplied by hydropower specialists Wiegert & Bähr Turbinen- und Stahlwasserbau GmbH from Baden-Wuerttemberg, who implemented the reference project on the opposite side of the globe in exemplary fashion. Equipped with three separate cleaning arms to significantly speed up the cleaning process, the machine had to be installed within a rather narrow time window to keep the power plant’s downtime as short as possible. Thanks to painstaking preparations, including an extensive system pre-assembly and test run in Germany, complemented by a perfectly coordinated on-site mounting process, the installation could be completed in record time.
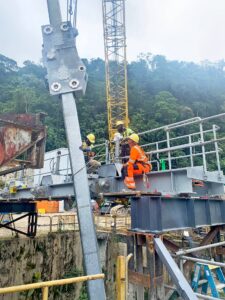
© Wiegert & Bähr
Known and appreciated beyond Germany’s borders as a competent small-scale hydropower partner, Wiegert & Bähr recently celebrated the successful completion of an international reference project. “From a German perspective, you can’t get much more international than that,” says Managing Director Markus Rest, commenting on the contract for the project in Papua New Guinea, the world’s third-largest island state after Indonesia and Madagascar. Essentially, the contract called for a complete refurbishment of a water screening system for the hydropower plant that supplies the operating power for the extensive gold, silver and copper mining operation in the local Ok Tedi mine. The mine takes its name from the nearby Ok Tedi river, which runs along the national border with the Indonesian part of the island.
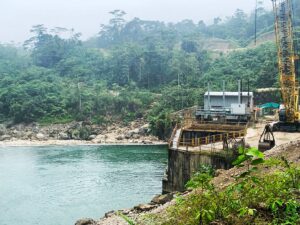
© Wiegert & Bähr
New partner ‘down under’
The contract for the Papua New Guinea project has a rather long pre-history, as Markus Rest explains. Metaval Consolidated Pty Ltd. is headquartered in northern Australia and focusses primarily on serving the energy and industrial sector. The company had been on the lookout for a new partner for the implementation of hydropower projects. Metaval had also contacted their German-based business partner to make enquiries about competent firms in the industry. As a result, Wiegert & Bähr was highly recommended by Metaval’s partner. “The first time I met Metaval’s CEO, Andrew Garland, was about five years ago, at an industry trade show in Munich. During our conversation, we agreed that we would showcase our product portfolio ‘down under’ soon after. In 2019, my colleague Bernhard Wallmeyer and myself boarded a plane to Australia, where we met with Andrew Garland and his Sales Director, Dale Eastick. Together we went on a tour of potential customers in the water supply and hydropower industries. Among others, we also visited the ‘Entura’ engineering office, which was busy refurbishing the screen cleaning system for the Ok Tedi Mine in Papua New Guinea. Back in Germany we worked out an optimised screen cleaning concept for the project, which we then offered to the customer,” as Markus Rest recalls.
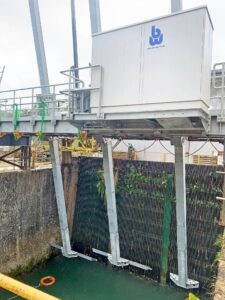
© Wiegert & Bähr
Single-step intake cleaning
The concept developed by the hydropower experts must have really struck a chord with the facility’s operators, as Wiegert & Bähr were already awarded the contract for the project in early 2021. As the company’s Head of Construction, Michael Wiegert, explains, “The old machine was running on rails to clean the screening area, which was segmented into three sections. Since the machine was only able to work on one section at a time, it took quite a long time to complete a full cleaning cycle. Our concept focussed on speeding up the cleaning process by using three telescope arms working in parallel to clean the entire screening area in one go.” Thorsten Vonthron, the project’s coordinator, names the time factor as one of the project’s key challenges: “While reconstruction work was going on in the intake area, the two turbines in the power house couldn’t be operated and had to be shut off. During this time, the operating power for the mine was supplied by a series of diesel generators. However, the high fuel prices meant that their use had to be kept as short as possible. So, delays during the installation of the new screen cleaners were a definite no-no, which is why great efforts were taken in advance to keep things going as smoothly as possible during the actual installation.”
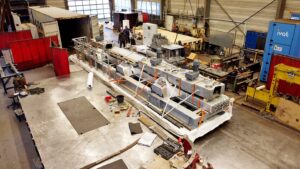
© Wiegert & Bähr
Test run in Baden-Wuerttemberg
The entire system was manufactured at Wiegert & Bähr’s headquarters in the small town of Renchen. Before it could be packed up for shipping (literally on the high seas), it had to be fully assembled at the production facilities and subjected to a series of trial runs. “When we designed the system we made sure that it could be delivered in a highly pre-assembled state so on-site installation would be as quick and straightforward as possible. So the central electrotechnical and oil-hydraulic components were all installed in an all-in-one switchbox, which was then mounted right on top of the structural steelwork of the machine. The mechanical construction was based on extra-durable gear racks that were suited to the required cleaning depth of around 11 metres,” says Michael Wiegert, adding that “the tropical climate in Oceania required certain special design details that wouldn’t have been an issue anywhere else in the world. For example, the electromechanical and hydraulic components had to be fitted with extra-high quality insulation to withstand the high levels of atmospheric humidity. In addition, some of the cable harnesses had to be fitted with additional protective sheathing to protect them against scavenging rodents.
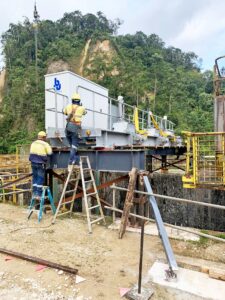
© Wiegert & Bähr
Flexibility is key
With factory acceptance testing completed, the system was packed into two shipping containers in February 2022 and shipped from Rotterdam Harbour to Brisbane. In the end it took around a month, including the required stopover in Singapore, for the shipment to finally arrive. In coordinating the final installation, Wiegert & Bähr had to prove their professional flexibility on more than one occasion. For one thing, the installation date, originally scheduled for early summer of 2022, could not be kept due to ongoing coronavirus protection measures. Once the pandemic restrictions were lifted, the installation was rescheduled for autumn the year before. However, due to the rising prices of the fuel needed for the emergency power supply units to sustain the mining operation, the installation had to be postponed yet again. It was not until late summer 2023 that the final installation could go ahead, implemented by Wiegert & Bähr technicians in cooperation with local experts. “Our guys had been in the country already three weeks before the official start of the installation to prepare for the installation in painstaking detail. In installing the system in the intake area, the technicians proceeded by assembling the required components for the facility right next to the old machine. With the obsolete equipment removed, it was finally time to lift the entire assembly towards the screening area with the help of a mobile heavy-lift crane, anchor it into place and take it into operation. Everything went very smoothly at the installation site, so I have to give high marks to our technicians and the on-site crew for a job very well done,” says project coordinator Thorsten Vonthron.
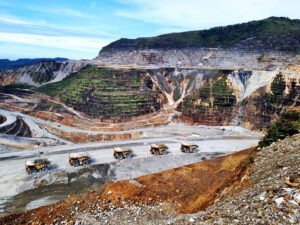
© Wiegert & Bähr
International contracts are most welcome
Managing Director Markus Rest is also very happy with the result of the first Wiegert & Bähr project on the opposite side of the globe: “Of course we’re thrilled to be able to win another international customer and partner with Metaval. It seems our project implementation made a good impression. Ever since the new screen cleaner was put in operation we’ve had nothing but positive feedback about its functionality and the practical experience gained during its operation. The huge effort behind the project, like the trial assembly, the test runs at our facilities, and the elaborate coordination of the project have definitely paid off. With this reference project to our name, I’m convinced it won’t be too long before we’ll be able to make our next international appearance.” That said, the Managing Director does not fail to mention that Wiegert & Bähr has already had the opportunity to prove its international competence in Africa. “We’ve been working as sub-contractors on the Nangbeto dam in Togo for more than three years now. It’s a long-term project, which has been prolonged even further due to the coronavirus pandemic, and it involves a complete revision of the hydraulic steelwork for a large hydropower facility that gets its water from the dam lake.”