Jettenbach-Töging power plant rebuild generates clean electricity for 200,000 households
The complete rebuilding of the Jettenbach-Töging Inn power plant in Upper Bavaria involved an investment volume of around €250 million, making it Germany’s largest hydropower project in the last few years. The VERBUND Innkraftwerke GmbH project encompassed the complete rebuilding of the weir in Jettenbach and machine house in Töging, each next to the original listed structure. The concrete seal of the around 20-km diversion channel at the plant, originally installed between 1919 and 1924, had to be raised by 70cm due to the required rise in the reservoir head. This renovation resulted in an annual energy production rise of about 25%, so the power plant now serves the annual electricity requirements of around 200,000 households on a sustainable basis.
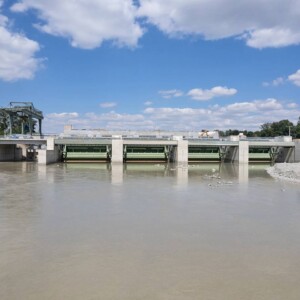
When completed in 1924, the Upper Bavarian Jettenbach-Töging plant was the first hydroelectric power station built on the River Inn, originally to generate electricity for an aluminium plant in Töging. A 6-span weir in Jettenbach dammed up the Inn, storing up to 340m³/s of works water for delivery to the powerhouse in Töging along a diversion canal approximately 20km long. This water drove 15 Francis turbines in the powerhouse to provide a combined bottleneck output at full capacity of more than 85MW. During renovation work on the Inn Canal in 2003, results showed that the smoother concrete applied in the renovation phase had increased flow capacity, suggesting potential for increasing electricity production during the summer months. In 2015, plans for expansion of the power plant, the central parameter of which was an increase in the expansion water volume to 410 m³/s, were submitted to the authorities at the Mühldorf District Office.
COMPLETE REBUILD THE BEST OPTION
“Several plant expansion options were considered prior to submission, including adapting the original machine building. The idea was rejected because it would have meant only very limited plant operation availability for several years, with considerable power generation losses. In addition, the existing structure is a listed building. This would have made large-scale technical modernisation extremely complicated. By completely rebuilding the power house next to the original building, the old plant continued to generate power, even throughout the construction phase, until it was finally shut down in September 2021”, explained Bernhard Gerauer, VERBUND’s overall project manager – adding that the approval procedure prior to project implementation had involved considerable effort. A further key aspect of the project was the construction of a new weir around 50m downstream from the previous location. Raising the weir head by 70 centimetres necessitated the extension of the concrete seal back up along the diversion route in the Inn Canal.
NEW WEIR SYSTEM
The new weir in Jettenbach is made up of four weir sections, each 26m wide and 9m high. The weirs are designed to be rotating segments with flaps attached. When in operation they have to withstand immense physical forces, particularly radial forces generated by the pressure of the water. These are exerted on the bearings positioned on both sides, and passed onto the structure. The stress amounts to around 6,700kN per bearing, and in the axial direction approximately 1,600kN per bearing. A water-powered screw with near-bottom and near-surface entry points was positioned on the orographic left side of the new weir to serve as a fish pass. “At 16.3rpm, the screw rotates slowly, thereby transporting fish safely down a height difference of 8.8m into the tailwater within a cushion of water. Whenever there’s weir overspill, fish will be able to descend directly over the weir,” says Bernhard Gerauer. The hydroelectric screw conveyor manages flow at 3m³/s, for a bottleneck capacity of about 200kW. In a normal year it can generate around 1.5GWh of electricity. The bypass channel, built as a fish ladder in 2003, was adapted to the new weir‘s target head.
SAILING MODE ENSURES SAFETY
The mechanical engineering sub-project manager at VERBUND, Christian Weichselbraun, reports: “The issue of safety had a major influence on the design of the three vertical-axis Kaplan turbines.” He emphasised that: “Essentially, it was a question of how the machines would be expected to react in the event of grid failures or large-scale blackouts. What would happen if we were no longer able to release the electricity onto the grid? If the guide vanes in the turbines closed within seconds while operating at full capacity, the worst case could see 410m³/s of works water create a backflow wave, leading to flooding along the diversion route. ‘Sailing mode’ was implemented to eradicate this risk. Basically, operating in sailing mode involves the removal of water through the rotating turbine without transferring power from the generator to the grid. To do so, the impeller is completely opened, while flow and speed control are governed by the guide vane. The braking force of the open impeller generates a speed increase of up to 120% of nominal speed. Energy potential is dissipated by pressure pulsations in the turbine caused by vortex formation in the bladeless space between the impeller and the guide vane. “The turbulence triggers strong vibrations and immense stress forces, especially on the suction pipe, impeller, shaft, lower turbine guide bearing and turbine cover. The machines had to be constructed and designed to ensure no damage would occur in such event,” outlined Christian Weichselbraun, adding that during commissioning the testing of all three machines was completed in sailing mode over a period of ten hours without any problems.
HIGHLY EFFICIENT KAPLAN TURBINES
The Slovenian manufacturer Litostroj Power manufactured three double-regulated Kaplan turbines for the project. All three of the turbines were identically built, and designed for a maximum water flow capacity of 136.7m³/s from a 35.5-m net head. Working at full capacity, each achieves a 46.2-MW bottleneck maximum. Adjustable runner blades and guide vanes enable the turbines to double-regulate and achieve maximum efficiency for a wide range of flow rates; even with a reduced water supply. The 6-blade impellers are manufactured from high-grade stainless steel, rotating at 166.7rpm in modulating mode and increasing to 200rpm in sailing mode. Installation of the respective turbine components was a multi-step procedure linked to construction progress at various sites within the power house. “The intricacy of the relationship between construction and concreting work when installing the electromechanical equipment was generally important for ensuring we kept to the project schedule” the two project managers confirmed. Each of the three machine sets in the powerhouse was fitted with a synchronous generator, directly coupled to the turbine runners, and with a nominal apparent power of 55MVA. Essential electrotechnical equipment, including generator protection and excitation equipment, medium-voltage switchgear elements, low-voltage distribution infrastructure, and the plant’s control technology, was supplied by Andritz Hydro.
SUCCESSFUL COMMISSIONING
One project milestone was reached on 21st September 2021 when the machines that had been in operation for almost 100 years were finally shut down in the old powerhouse. “We’d been working towards this date for years” stated Bernhard Gerauer. “Decommissioning the old machines enabled us to finish the remaining construction work and complete the concreting of the intake area at the new power house.” Excitement began to build a few months later when wet commissioning commenced at the new plant on 1st February 2022, as Christian Weichselbraun explains: “Starting up the machines for the first time was a key moment, as water could have leaked from the structure or the any of the numerous seals. Fortunately, we were spared any major leaks and the start-up was a success.” Over the following months the new plant was tested extensively, and the various ‘teething troubles’ that inevitably occur in a project of this magnitude were eliminated. By mid-June the plant was ready to go into regular operation.
DECISION TO RENEW PAYS OFF
In conversation with zek HYDRO, both of the project managers drew a thoroughly positive conclusion on the project. “We‘d be happy to do it all over again” says Bernhard Gerauer. “We had the luck that goes with hard work. The entire project was completed within the estimated cost and time frame, which is not a matter of course. It’s important and satisfying to note that no serious accidents occurred during the construction phase.” As Christian Weichselbraun confirms, the success of the project was due to an exemplary team effort. “Cooperation between the VERBUND team, suppliers and construction companies all went very smoothly. Whatever schedule clashes, multiple technical and construction problems came up – they were all solved in a cooperative manner.” The plant commissioning ceremony was held on 30th September 2022, around four years after commencement of initial construction work. Several high-ranking representatives of politics and business attended the ceremony in Töging. In his speech, Bavarian Prime Minister Markus Söder underlined Bavaria’s leadership in the field of renewable energies: “Hydropower is genuine home-grown energy. Here, green electricity is generated for 200,000 households with a-hundred-year-old infrastructure. Bavaria is Germany’s hydropower state, with a total of 4,200 small and large-scale plants generating electricity for four million households. We firmly believe in the value of hydropower and are continually expanding in this field.”