Large-scale South African farmer relies on German hydropower expertise for a third time
The South African farmer Michael Vermaak has become a loyal and regular customer for Ossberger, the German hydro-industry experts. Since 2008, three small hydropower plants have been built on the expansive Klipfontein farm in the village of Cookhouse. All three have been equipped with comprehensive Ossberger electromechanical packages. The latest plant went online for the first time in September 2023 with another one of Ossberger’s high-performance technology packages – including a crossflow turbine with a bottleneck capacity of 412 kW, and all the electrical fittings and control equipment. Furthermore, at the oldest plant all the control technology was updated. Resultantly, all three power plants can now operate as island solutions or in parallel grid operation – and each one is equipped with black-start capabilities.
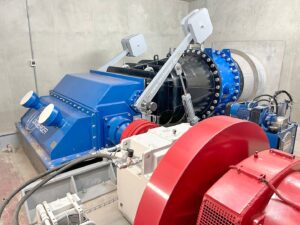
© Ossberger
Anyone in South Africa self-sufficient enough to meet their own electricity needs with a proprietary power plant can count themselves very lucky. So-called ‘load-shedding’ is part of everyday life for around 60 million inhabitants in the southernmost country on the African continent. Power cuts can last up to twelve hours, with entire regions and cities being taken off-grid. According to ESKOM, the state-owned energy supplier, South Africa’s power supply would collapse completely without load-shedding. Corroborative media reports suggest that a major reason for the problematic situation is the generally desolate state of the country’s energy infrastructure, resulting from decades of mismanagement and corruption.
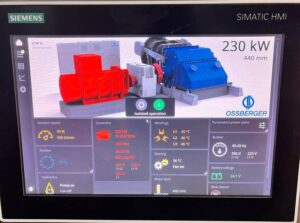
© Ossberger
Klipfontein farm is self-sufficient
Having taken matters into his own hands in 2008, building a small hydropower plant on his extensive Klipfontein Farm property in the village of Cookhouse, Eastern Cape Province, the nationwide energy supply problem is no longer a cause for concern for Michael Vermaak. The plant utilises the hydro-energetic potential of an irrigation canal branching off from the local Fish River, and supplies water to a number of farms. Acquisition of additional properties enabled the operator to expand his farm and led to increased demand for energy. In response, in 2018 a second hydropower plant was built and commissioned, and in September 2023 a third plant went into operation.
Ossberger supplies reliable solutions
Ossberger crossflow turbines have been in use worldwide for over 100 years and the expertise of these German industry specialists was the operator’s first choice from the first plant on; and for the full range of technical hydropower plant infrastructure – machine sets, hydraulic steel structures, electrical fittings and control technology. Christian Habermann, Ossberger’s Technical Director explained: “Generally, South Africa is a favourable market for us, and in our experience, Ossberger turbines are particularly appreciated by operators of systems on irrigation channels as on Klipfontein Farm. The objective for a basic crossflow turbine is not to harvest the last possible percentage point of its efficiency potential, but to deliver electricity reliably and uncomplicatedly. This is the core characteristic of our solutions and, ultimately, something our customers consider to be particularly important.” The small hydropower plants in Cookhouse generate electricity for energy-intensive agriculture, and to feed into the public grid. A significant proportion of the electricity generated is directed to a pumping station with several variable-speed pumps. The station is used mainly during the night to fill a reservoir excavated from a hillside for the irrigation of surrounding farmland.
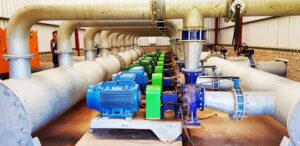
© Ossberger
Multi-modal operating equipment
The first plant, built in 2008, was designed purely for island operation. Now, however, all three power plants can operate in island and grid-parallel modes, and all have black-start capabilities. Ossberger’s scope of delivery for the latest hydropower plant in Klipfontein consisted of the crossflow turbine, gearbox and synchronous generator, the flywheel, the butterfly valve and all electrical and I&C equipment. The horizontally-fed crossflow turbine is designed to achieve a discharge water volume of 2.5 m³/s with a net head of around 20 m, for a bottleneck output of 412 kW under full load conditions. Drive water for the turbine is provided via an underground penstock pipeline connected to a newly-built inlet on the irrigation canal. No separate screen cleaning machine was installed at the inlet area. However, Christian Habermann explained that, if required, such a machine could be retrofitted without great effort. After driving the turbine, the headrace water is returned to the diversion channel and, after a short distance, flows into the Fish River. Plant construction took around a year and was completed in autumn 2023. The operator and several local companies played an active role in the plant construction phase. The machine building is completely subterranean, and assembly of the electromechanical equipment and cabling laying were tasks conducted by local labour teams. Ultimately, the power plant was commissioned in September 2023 under the supervision of an Ossberger technician.
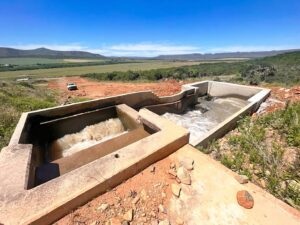
© Ossberger
Three is the magic number
Operation of the state-of-the-art system is fully automatic. The control system can be accessed using touch panels installed in the machine buildings, or accessed online via smartphones and PCs. As well as being experts in the construction of turbines, the German all-rounders at Ossberger demonstrated their hydropower expertise by providing the full scope of control technology for the plant network. “In the course of order implementation it was also necessary to modernise the electrical engineering in the oldest power plant. As a result, all three plants can now generate electricity individually, or combine automatically to form a completely syn- chronised network, depending on the current requirements”, Ossberger’s Area Sales Manager Markus Sauerbeck told us. Christian Habermann summarised: “The entire project went very smoothly, and coordination and communication were flawless. It was de- finitely of benefit to be familiar with each other from previous projects, and to be able to form a well-oiled team. We are certainly in a good position to implement further projects in the field of agricultural or municipal irrigation systems. The Cookhouse project is a good example of how an existing irrigation channel can now be used three times to generate clean electricity.”