Austrian industrial service providers confirm their reputation as an expert hydropower partner
Bilfinger Industrial Services GmbH is one of Austria’s largest industrial service providers, and a major European problem-solver when facing challenging hydropower plant construction tasks. The company recently demonstrated its expertise in the Swiss canton of Valais. The company from Upper Austria was commissioned for a partial refurbishment of the penstock at Nendaz power plant near the town of Sion – the largest open-air penstock in Switzerland. The challenging renovation project was completed in summer 2022 after around 2.5 years of hard work.
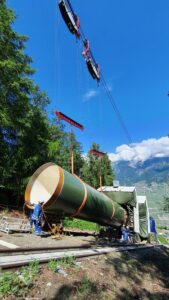
© Bilfinger / Erich Reiser
Normally, around a fifth of all energy stored in Switzerland is sourced from Grande Dixence reservoir in the canton of Valais. The reservoir holds a total capacity of around 400 million cubic metres of water processed in two stages to optimise energy yield. The first stage is Fionnay power station at 1,490 metres above sea level; the second at Nendaz power station 1000 metres further downhill. If the power plant at Bieudron is also added to the output of the two plants, as it also utilises the reservoir via its own penstock, the entire power plant complex achieves an impressive total output of 2,000 MW. State-of-the-art technological infrastructure enables it to supply the grid in a mere 4 minutes with an amount of electricity equivalent to that provided by an average nuclear power plant in the same period. Grande Dixence SA operates the plant as one of the European market’s leading providers of electrical power. Grand Dixence SA is under shared ownership: Alpiq (60%), Axpo (13.3˙%), Repower, BKW (13.3˙%) and IWB (13.3˙%).

© Bilfinger / Erich Reiser
A penstock that inspires superlatives
The headrace connecting the two power plants in Fionnay and Nendaz is long. The tunnel conduit for the headrace water is 16 km in length, taking it to an equalisation basin around 1,000 m above the Nendaz control centre. Here, an 890-metre section of penstock connects to the powerhouse on the Rhône plain, and had served reliably for almost 60 years. However, the penstock section from the Peroua throttle valve to the transition into the vertical shaft now required complete replacement as part of a proactive maintenance initiative. Once dismantling of the old pipeline had begun in March 2020, a month later the renowned Austrian industrial services providers at Bilfinger Industrial Services GmbH received an order from Grande Dixence SA to replace the above-mentioned section of pipeline. The penstock is an exposed pipeline braced by ring supports. The 890-metre section has a diameter of 3.15 metres. As regards pressure and diameter parameters it’s the largest exposed penstock in Switzerland.
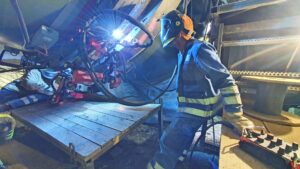
© Bilfinger / Erich Reiser
Engineering phase marks project commencement in June 2020
“Compared to a new construction project, every refurbishment project poses specific challenges. In this case they included the question of how to reuse the existing concrete supports for the ring braces and the foundations for the elbows. Erich Reiser, Bilfinger’s appointed project manager, explains: “These challenges were factored into our planning considerations.” The 32 supports and 7 fixed points were incorporated into the structural planning of the system to ensure they bore ideal loads during normal operation. To guarantee this occurred in practice, in addition to temperature and pressure development, tolerances were also considered when planning the new penstock. Scheduling requirements made it necessary to procure materials quickly in parallel with the engineering implementation. Sheet metal was rolled on demand for construction and delivered to the manufacturing facility in Wels, Upper Austria, from November 2020. Production of the manifolds commenced here early on as they required the longest lead time. External and internal anti-corrosive protection was already applied in the factory, except to the intended weld seams required for connection during assembly. The construction site was set up very quickly and ready in March 2021. The construction site was spread over an area between 1050 m and 1400 m above sea level on the northern slope of Dent de Nendaz. The old pipeline had already been dismantled and removed using a cable car, and transported away by lorry.
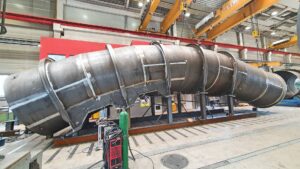
© Bilfinger / Erich Reiser
High-pressure pipeline assembly
A purpose-built ropeway conveyor with a load capacity of 20 metric tons was set up for construction work, serving around 90% of the site. It played an important role in the assembly stage as many sections were not accessible for mobile cranes. Certain sections ran through wooded areas or, at a gradient of 100%, were so steep that the cable conveyor was the most viable means of installation support. Another challenge was posed by the very limited availability of construction site storage areas. “The little storage space available had to be cleared artificially by moving earth, demanding complex logistics to guarantee just-in-time delivery of components from Austria right after anti-corrosion coating had been applied at the factory,” recalls Erich Reiser. Assembly was carried out starting at the elbows and working upwards. The elbows were determined as fixed reference points on the way to the top. Two site sections for assembly work were situated very close to the village of Les Condémines. All of the assembly platforms were fitted with a sound-absorbent shell for the local population to minimise noise pollution generated by cutting, grinding and welding during assembly work.
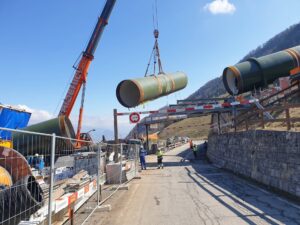
© Bilfinger / Erich Reiser
All challenges mastered
Approximately 10 % of the site in the lowest section of the construction area could not be accessed using the cable conveyor, so a special gantry crane was devised to serve this section and enable the lowest curve manifold to be positioned on the vertical shaft. Subsequently, the gantry crane was used to install all the other pipe sections. Particular attention was necessary when routing, assembling and welding the pipeline across a local road. Nevertheless, this was all achieved without disrupting traffic. After a 14-month construction phase the Bilfinger Industrial Services GmbH team ultimately completed the section in May 2022.
On-site application of the anti-corrosion coating also began at around the same time. Work on the joining weld seams inside the pipeline was carried out from specially erected platforms. The winch required for positioning was located in the throttle valve house. A total of four platforms were transported with the ropeway cable conveyor – section by section – to complete external anti-corrosion coating. This was sealed with a full top coat of paint in order to give the pipeline a uniform appearance.
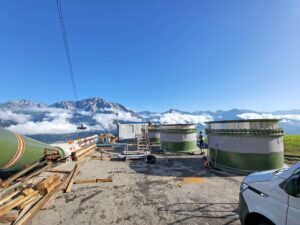
© Bilfinger / Erich Reiser
Wet trials from autumn 2022
In July 2022, the steel structure installation was completed on the installation of six expandable sections below the fixed positional reference points. The expansion joints adapt to motions caused by forces exerted during operation, and also compensate for terrain subsidence. The customer fitted the entirety of the exposed penstock with sensors, so now the fascinating readings can be subjected to analysis. These measurements reveal details of the effects of forces exerted during the various operating modes at the power plant, as well as of external influences on the steel penstock – such as the position of the sun.
The renovation project was completed and handed over to the customer, Grande Dixence SA, for trial operation after an overall duration of around 2.5 years. The entire penstock was refilled with water in early September 2022, and the first machine groups went back into operation at the beginning of 2023.
Broad-based value chain
Bilfinger Industrial Services GmbH once again demonstrated extensive experience and hydropower expertise when fulfilling the Grand Dixence SA order. Bilfinger has its headquarters in Linz, and subsidiaries at nine other locations in Austria and neighbouring countries, making it one of Austria’s largest industrial service providers. The company’s service portfolio covers the entire value chain – including advisory services, engineering, manufacturing, assembly, maintenance, plant expansions and general overhauls, environmentally-friendly technologies and digital applications. Over the decades, Bilfinger has earned an excellent reputation as a reliable partner, having worked on large numbers of hydropower-sector projects in Germany and further abroad.