Bavarian Specialist supplier of complex formwork for modern hydropower projects
Today, Mitterfelner Schalungsbau from Bavaria has completed more than 200 hydropower projects, and is considered the ‘go-to’ manufacturer of special formwork for hydropower plant construction. The company has supplied suction pipe formwork, bend, inlet and cone formwork, and also inlet spiral chamber formwork, since 1996. The construction of timber components is sometimes very complex, and requires a great deal of experience and finely-honed craftsmanship. Mitterfelner’s formwork is environmentally friendly, and guarantees optimal flow due to minimal surface roughness. Modern connecting systems enable large formwork components to be dissembled into smaller sections for international transportation via trucks and containers.
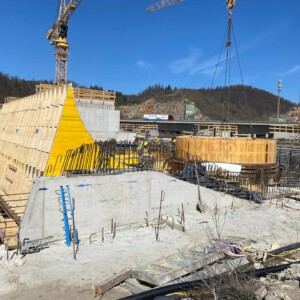
Without doubt, the special wooden formwork components for elbows, suction pipes and intake spirals, are some of the most spectacular items that can be seen on a hydropower construction site. Shapes are clear recognisable very early on in the construction phase, thus revealing the route the water will take through the power plant. Despite their imposing appearance, these components are products of an enormous amount of expertise and experience. Shaping concrete with formwork is still one of the more demanding tasks for hydropower projects. After all, these are usually round, curved, twisted shapes with varying radii that can’t simply be produced as standard components. On the contrary, they really are bespoke items, tailored site conditions to the greatest possible degree. Very few companies are able to meet the multifaceted requirements of special formwork construction for modern hydropower plants. However, Mitterfelner Schalungsbau from Obermünchsdorf in Bavaria is one such business, having been active and very successful in this field since 1996. Today, the company accompanies customers along the entire project chain, from planning to manufacturing, to on-site formwork assembly.
Demand for craftsmanship
Robert Prielmeier, Managing Director at Mitterfelner Schalungsbau explains: “Planning has evolved greatly over the past decades. The old 2D planning techniques have long since been replaced by modern 3D CAD programmes. Now, in some cases, we use 3D models from the printer for a better standard of visualisation. It is essential for us to be familiar with all common CAD programmes, as the requisite formwork design is usually pre-defined by each turbine builder’s construction specs. That’s why today we also have graphic drafting programmes with more than 60 interfaces to all the most commonly-used CAD programmes on the market.” Regardless of the degree of planning tool sophistication, human expertise remains indispensable for implementation. Extremely complex bespoke formwork is made largely by hand. “Each component has different radii, curvatures and shapes – and this demands craftsmanship and skill,” adds Prielmeier, pointing out that building formwork is a core activity of the joinery and carpentry trades, and admitting that although, for this reason, apprentices at Mitterfelner Schalungsbau are still trained in these trades, it is becoming increasingly difficult to find young talents.
The central issue of sustainability
Mitterfelner Schalungsbau’s particularly high standards of expertise in the production of special formwork for hydropower plants can be explained by the fact that the founding family has operated its own hydroelectric power plant for several generations. Hydropower is, so to speak, in Mitterfelner’s DNA. In 1996, the company conducted a thorough conversion of its own hydropower plant, thereby determining the direction of the company’s commercial development moving forward. Managing Director Prielmeier expands: “That’s also why the idea of environmental sustainability plays such a big role for us, and why we still rely on natural, untreated wood from locally felled timber.” This makes good sense, particularly if the issue of disposal in the construction industry is considered more closely. Prielmeier draws the comparison with tunnel construction – in which other types of formwork skins are often used. Once these have been contaminated with cement slurry, they have to be disposed of in a very time-consuming and expensive manner, whereas disposal of Mitterfelner’s wooden formwork is relatively simple. Indeed, after use the elements are often cut up for use as firewood. Robert Prielmeier explains the advantages of untreated wood in more detail: “Wood extracts water from concrete, resulting in fewer air pockets and cavities – making it harder and more resistant.” In some cases, if structural conditions permit and the customer wishes so, formwork can be used multiple times. The formwork is solidly braced in the factory, so it’s ideally suited for re-use.
Optimum flow conditions
Not uncommonly, on-site spatial conditions at a power plant are too awkward to allow the insertion of formwork en bloc. In such cases, it is essential to include the option of dissembling formwork into smaller sub-units. To guarantee this flexibility, Mitterfelner Schalungsbau deploys a functional and robust connection system to enable simple and safe assembly and disassembly. Divided in this way, formwork components can be transported over long distances in trucks or containers, and be reassembled on reaching the construction site. Nowadays, every hydropower operator attaches the utmost importance to optimising flow conditions within the plant. The smoother the surface of a water channel along which the works water flows, the smaller the loss of energy via friction, and the greater the efficiency and profitability of the power plant – be it the surface of a penstock or an intake spiral. Mitterfelner pays special attention to the outer surface of the formwork, filling pores and sanding it with fine sandpaper. Ultimately, the meticulous and precise approach to preparation pays off, not least because the majority of hydropower operators in Central Europe rely on the special formwork manufactured by Mitterfelner Schalungsbau. The successful completion of more than 200 projects bears reference to the quality of this work. Mitterfelner Schalungsbau’s expertise can be marvelled at in a whole range of hydroelectric power plants – in high-alpine pumped-storage power plants, such as the Obervermuntwerk in Vorarlberg, small and innovative shaft power plants in Bavaria, and large run-of-river power plants on the Inn and Mur rivers.