Hydropower 4.0 – implementing imagination
VERBUND is pioneering the hydropower plant of tomorrow – today, in the Styrian village of Rabenstein, analysing the efficacy of concepts such as ROVs, smart glasses, digital twins and the future of servicing – predictive maintenance. Anyone gazing down the Mur river valley towards Graz from the rocky hillside in Frohnleiten can imagine the journey in time from the Middle Ages into the 3rd millennium. Rabenstein castle, built on a rocky outpost in the 12th century, towers above the valley as, further down the river, a remote operated underwater vehicle (ROV) is lowered into the water to make an extremely precise approach towards the runner of the approximately 100-metric-ton tubular turbine at the hydroelectric power plant. Anomaly detectors transmitted sensor data from the machine group and triggered the alarm, having detected an immense curtailment of the expected working life of essential parts fitted in the digital twin. The operational engineers reacted without delay, immediately shutting down the turbine to conduct a quick inspection. This was carried out by a real-time 3D sonar unit, eliminating the need to send divers on dangerous exploratory missions to examine the inlet basin of the machinery in freezing-cold water. The sonar can operate without restrictions in murky water, navigating unproblematically via acoustic signals, however poor the visibility for divers, and providing a glimpse of work in tomorrow’s hydroelectric power stations.
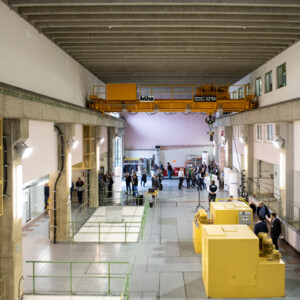
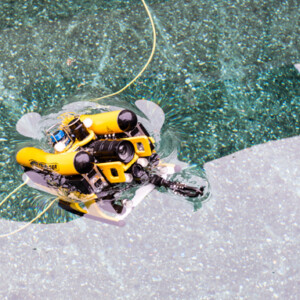
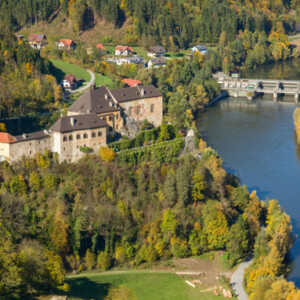
DIGITAL INTELLIGENT
What may sound futuristic – is increasingly becoming reality at VERBUND’s Styrian Rabenstein Mur river power plant. The run-of-river plant first went online in 1987. Since 2018 it has assumed a unique role in Europe as a venue for the implementation of pioneering digital technologies. Achim Kaspar, VERBUND board director responsible for digitalisation and production, explains: “We aim to evaluate every imaginable application of digitalisation in hydroelectric power stations to test the most promising technologies intensively at our pilot plant and implement them successfully at all Verbund operations.”
In Rabenstein, Project Manager Bernd Hollauf and his team are working with the concerted support of the station’s team on the testing of a dozen applications that bring together the fields of automation and intelligent data processing. For VERBUND the goal and the road ahead are as clear as they are challenging – to evaluate the most promising technologies at the pilot plant and test them to their limits. The variety of technologies in question ranges from intelligent sensorics, predictive models, digital twins, mobile assistance systems, pioneering autonomous surveying and inspection concepts – to interconnected platform solutions.
EFFICIENCY WITH FORESIGHT
Intelligent part-acoustic surveillance systems with AI capacities are to be used to provide data that form the basis of anomaly detection and prognosis models – to detect potential machine break-downs. Digital twins process sensor data in real-time simulations to predict the remaining working life of important machine components, as well as exploring the possibilities of other operational uses – and their effects. The buzzword for this potential is predictive maintenance and it’s the future of industrial servicing and repair. Predictive maintenance can remove the limitations of reactive approaches – responding when a break-down has already occurred, and of preventative maintenance – requiring preventative measures according to inflexible timetables. Predicting failures enables the active interception of impending breakdowns and damages, and the optimisation of plant efficiency. In a hydropower plant this is particularly beneficial as regards generators and turbines. As essential components in the process of electricity generation they are required to work reliably and without interruptions, since any kind of downtime or damage can result in an immense loss of productivity. An innovative inspection system uses a camera in combination with artificial intelligence to register negative changes within the generator before they become critical.
PROACTIVE PRODUCTIVITY
The benefits of predictive maintenance are obvious as the ideal moments for repair and maintenance activities can be scheduled before problems occur. This means service staff and spare parts can be deployed efficiently, and the losses of profit caused by machine downtimes can be eradicated. In terms of maintenance, staying ahead of the game enhances overall machine performance and the working life thereof. Another key positive is that any changes to the plant’s modes of operation, and the ways in which they burden components, can be fed into the digital twin to calculate the effects on parts in advance. This gives plant operations greater transparency – and the reduction in power station downtimes and breakdowns will lead to greater power supply reliability. When there are unavoidable service failures, mobile assistance systems can provide all the information necessary for repair work to the respective power station in real-time. The uses of tablets, smartphones and smart glasses are all being explored within this context at the Rabenstein plant. Overall, the plan is to realise completely new means and modes of troubleshooting; ones with which plant operatives can use their mobile devices to gain access to all the relevant data on a specific part of the plant, request and receive assistance from colleagues online, and digitally document the entire procedure on site. The question of whether smart glasses or tablet technology prevail here has not yet been resolved.
HYDROPOWER 4.0
A key point of emphasis at the pilot plant is the insistence upon partnerships with the industrial sector in the field of development, and on international cooperation agreements with manufacturers and research facilities. The work being promoted in Rabenstein is part of VERBUND’s broad cross-section of efforts towards automation and digitalisation; a field in which it is a European pioneer. The work encompasses the documentation of items such as central operational data records, remote control of all 131 power plants, automatic status monitoring of key electrical and mechanical components and the optimisation of machine usage. VERBUND is now managing and observing a wide range of aspects of everyday plant activity, partly via mobile devices – including seamless online surveillance of dam walls, digital recording of surveying and hydrography data, and also SAP-backed maintenance planning and implementation. Back in 2018, a multi-million digitalisation package was initiated on the road to the ‘transparent hydropower plant’. The objectives are the harmonisation of operational and maintenance processes, their digital portrayal, simplification of the work done in power stations, eradication of the jumps made from one medium to another (Digital Workforce Management), and the gradual implementation a Rabenstein-type digital power plant concept at other VERBUND sites. “Hydropower is very technically sophisticated, but it’s obvious there’s still potential for further improvement. We’re rethinking the hydropower concept with our digital power plant to serve this goal, to be ready to face future challenges, and to be armed to meet the requirements set by the energy transition ahead,” states Achim Kaspar succinctly. Digitalisation is a tool for reducing the difficulties and raising the efficiency levels involved in such work. However, skilled expertise and specialised planning know-how will continue to be indispensable; a requirement as abiding as the view of the castle high on the hill.